When machining slender shafts, challenges such as deformation, vibration, and increased cutting difficulty often arise. To ensure the machining quality, the following points should be carefully considered:
Lack of workpiece rigidity:
Slender shafts usually have poor rigidity and are prone to deformation or vibration. Use steady rests or follow rests to support both ends or the middle of the shaft to increase rigidity.
Consider segmental machining to reduce shaft deflection and minimize deformation.
Tool selection:
Use sharp tools to reduce cutting forces and lower the risk of workpiece deformation.
Increase the rake and relief angles appropriately to reduce friction and heat during cutting, thus minimizing thermal deformation.
Cutting parameters:
Reduce cutting depth and feed rate to lessen cutting forces.
Increase spindle speed appropriately and optimize cutting speed based on the material properties of the slender shaft.
Use of cutting fluid:
Adequate application of cutting fluid helps cool the tool and workpiece, preventing thermal deformation due to heat buildup.
Clamping method:
Apply reasonable clamping force to avoid workpiece deformation caused by excessive force.
Use soft jaws to provide even and gentle clamping pressure on the slender shaft, preventing surface damage and deformation.
Avoiding resonance:
Adjust the machine’s cutting frequency to avoid resonance between the workpiece and the tool.
Add anti-vibration devices or adjust the feed direction to reduce the impact of vibration on the workpiece surface.
Process planning:
Perform rough machining first to remove most of the material, then follow with finish machining to reduce the impact of deformation during roughing.
During finish machining, apply low-stress cutting to further control workpiece deformation.
By following these measures, deformation and vibration during slender shaft machining can be effectively controlled, ensuring machining precision.
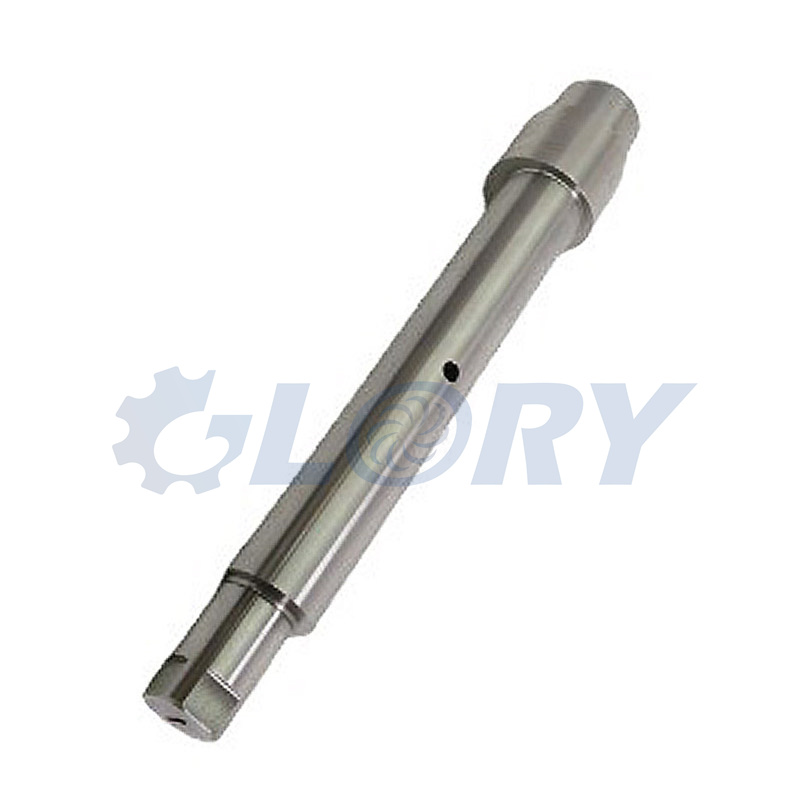