Our company provide OEM machining POM according to customer’s drawing.
POM (Polyoxymethylene), commonly known as Delrin or acetal, is a high-performance engineering plastic widely used in the manufacturing of precision components such as gears, bearings, pulleys, and connectors. While POM is favored for its high strength, low friction, and excellent wear resistance, it presents certain challenges during machining that require special attention. Below are the main challenges and key points when machining POM.
Challenges:
- Thermal Expansion and Sensitivity to Heat
POM tends to expand due to frictional heat during machining, which can affect dimensional accuracy and even cause parts to go out of tolerance. Excessive heat can also lead to the decomposition of POM, releasing harmful gases and posing safety risks in the machining environment. Therefore, controlling the temperature rise during machining is a major challenge. - Stress Release and Deformation
During the machining process, the cutting stresses accumulated in POM can cause stress release, leading to warping or deformation of the workpiece. This is particularly noticeable when machining thin-walled parts or larger components, which can compromise the final product’s accuracy. - Surface Quality Control
POM is prone to producing burrs and chip buildup during machining, which can affect the surface finish and precision of the parts. If the cutting tool is not sharp or if improper cutting parameters are used, the problems of burrs and rough surfaces will worsen. Moreover, POM chips are sticky and tend to adhere to the cutting tool, increasing tool wear. - Moisture Absorption
Although POM has relatively low moisture absorption, in environments with high humidity, it can still absorb moisture, leading to dimensional changes that affect machining accuracy. Additionally, in subsequent use, POM parts exposed to high humidity may experience size variations and a decline in mechanical performance.
Key Points in Machining:
- Optimizing Cutting Speed and Feed Rate
To reduce heat generation during cutting, it is recommended to choose appropriate cutting speeds and feed rates. Typically, moderate cutting speeds and larger feed rates help reduce frictional heat while maintaining machining efficiency. Also, reducing continuous cutting time to allow the workpiece to dissipate heat can help prevent excessive temperature rise. - Tool Selection and Maintenance
When machining POM, it is crucial to use sharp tools with suitable geometries. Tools with a large rake angle can help reduce cutting forces and frictional heat. To minimize chip adhesion, it is advisable to use coated tools or regularly change tools to maintain sharpness, thus improving machining efficiency and surface quality. - Proper Use of Coolant
Using coolant effectively can significantly lower machining temperatures, preventing material deformation or degradation due to excessive heat. For POM, using low-viscosity coolants with good lubrication properties helps carry away chips, reduces tool wear, and enhances surface finish. - Appropriate Clamping Techniques
To avoid deformation during machining, appropriate clamping methods should be used to prevent excessive clamping forces. For longer or thinner POM workpieces, using multi-point support or flexible fixtures can reduce the risk of deformation. - Post-Processing and Dimensional Stability
After machining, POM parts often require post-processing such as deburring or annealing to eliminate stress generated during machining and improve dimensional stability. If POM parts are to be used in high-humidity environments, environmental simulation testing should be performed to ensure long-term dimensional and performance stability.
Our Machining POM Part
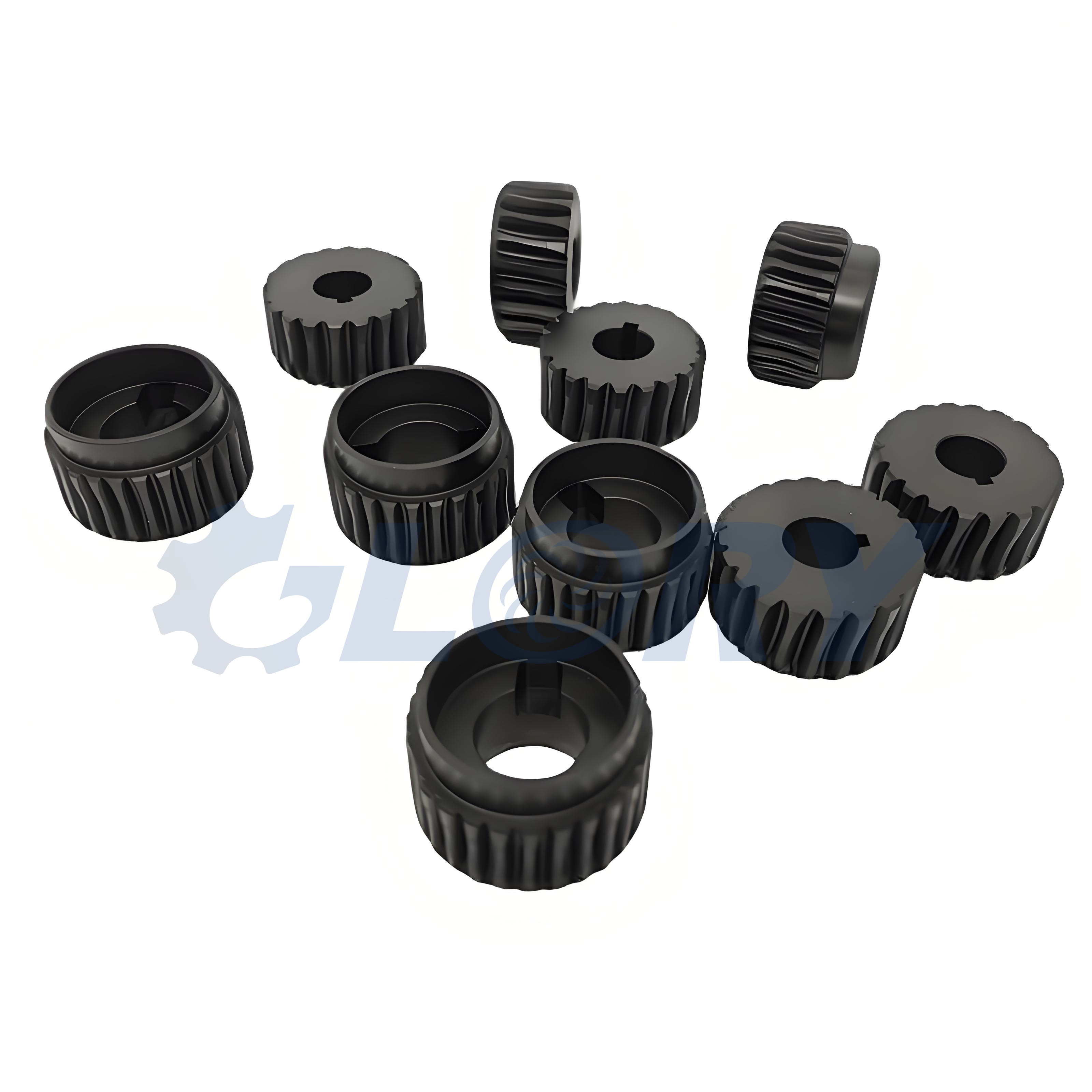
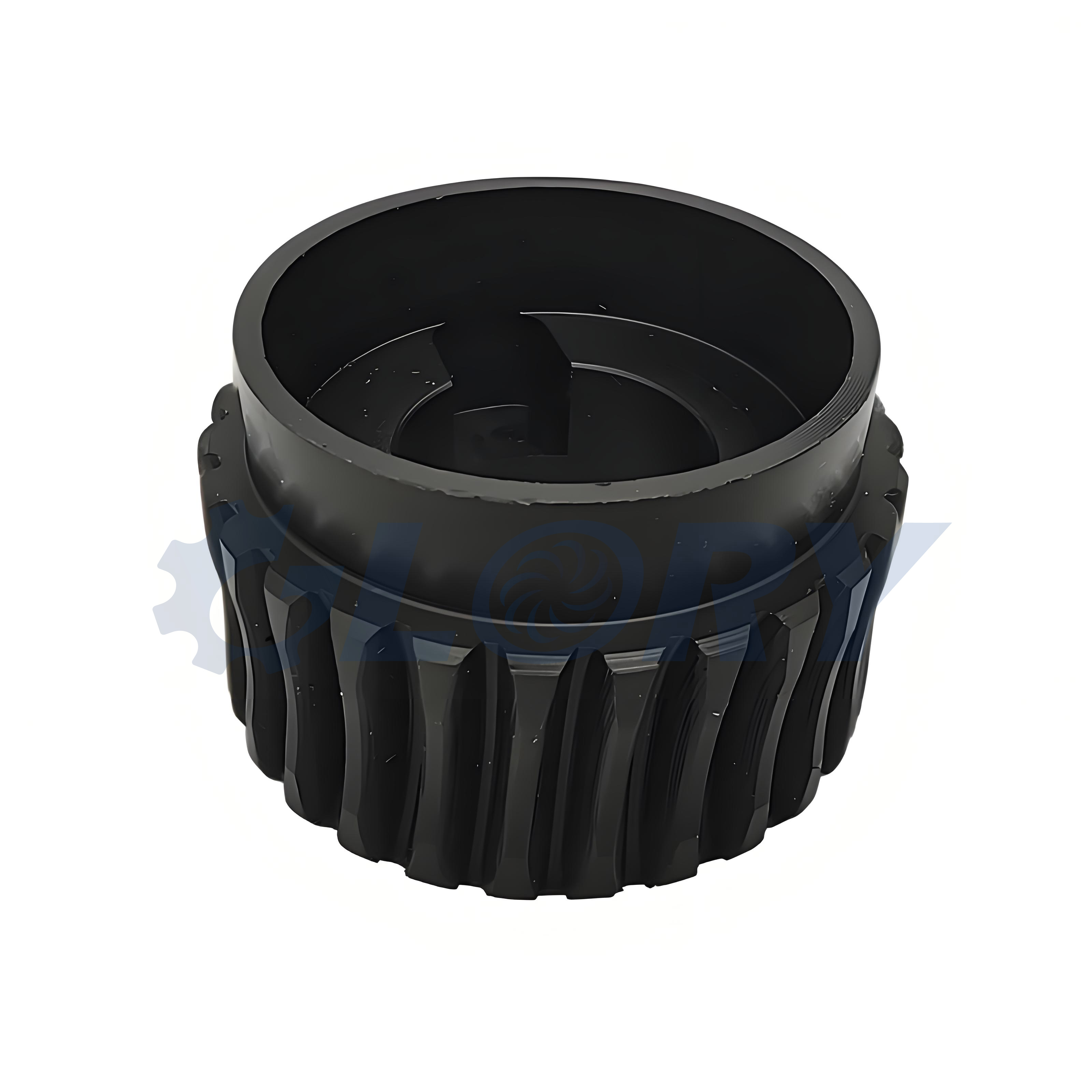
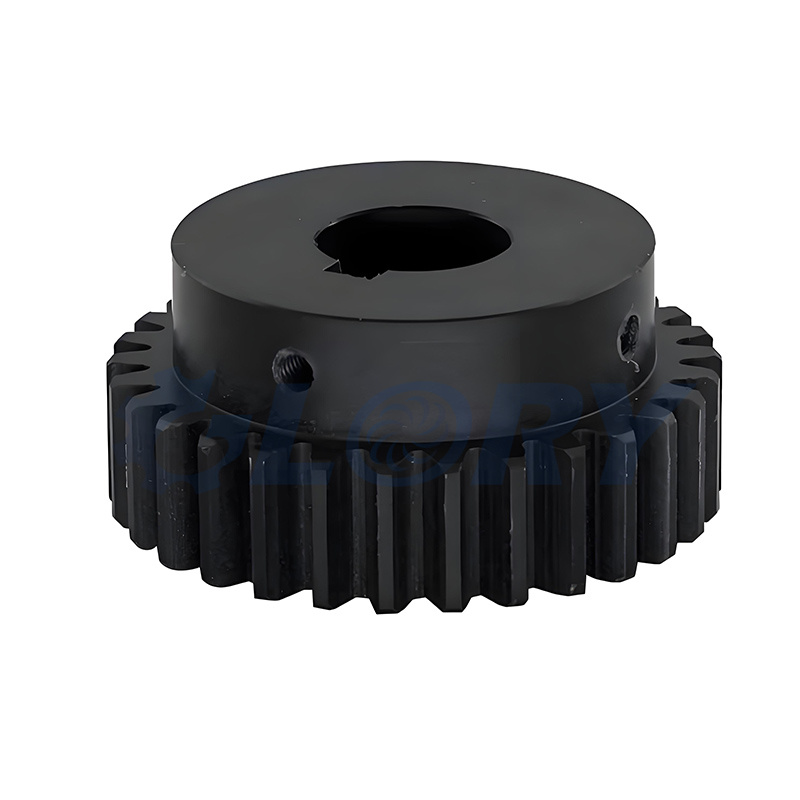
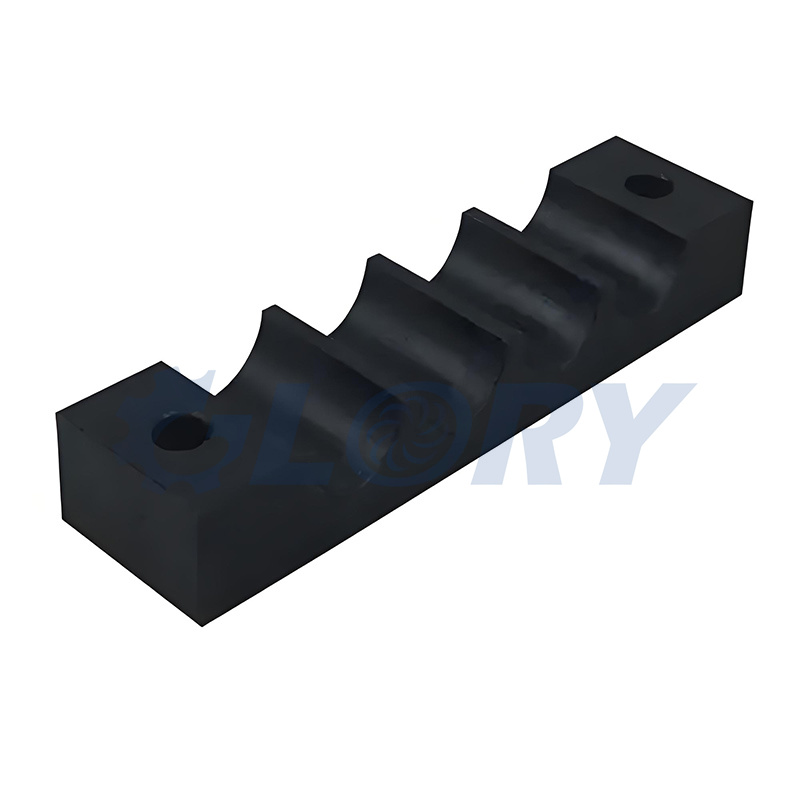
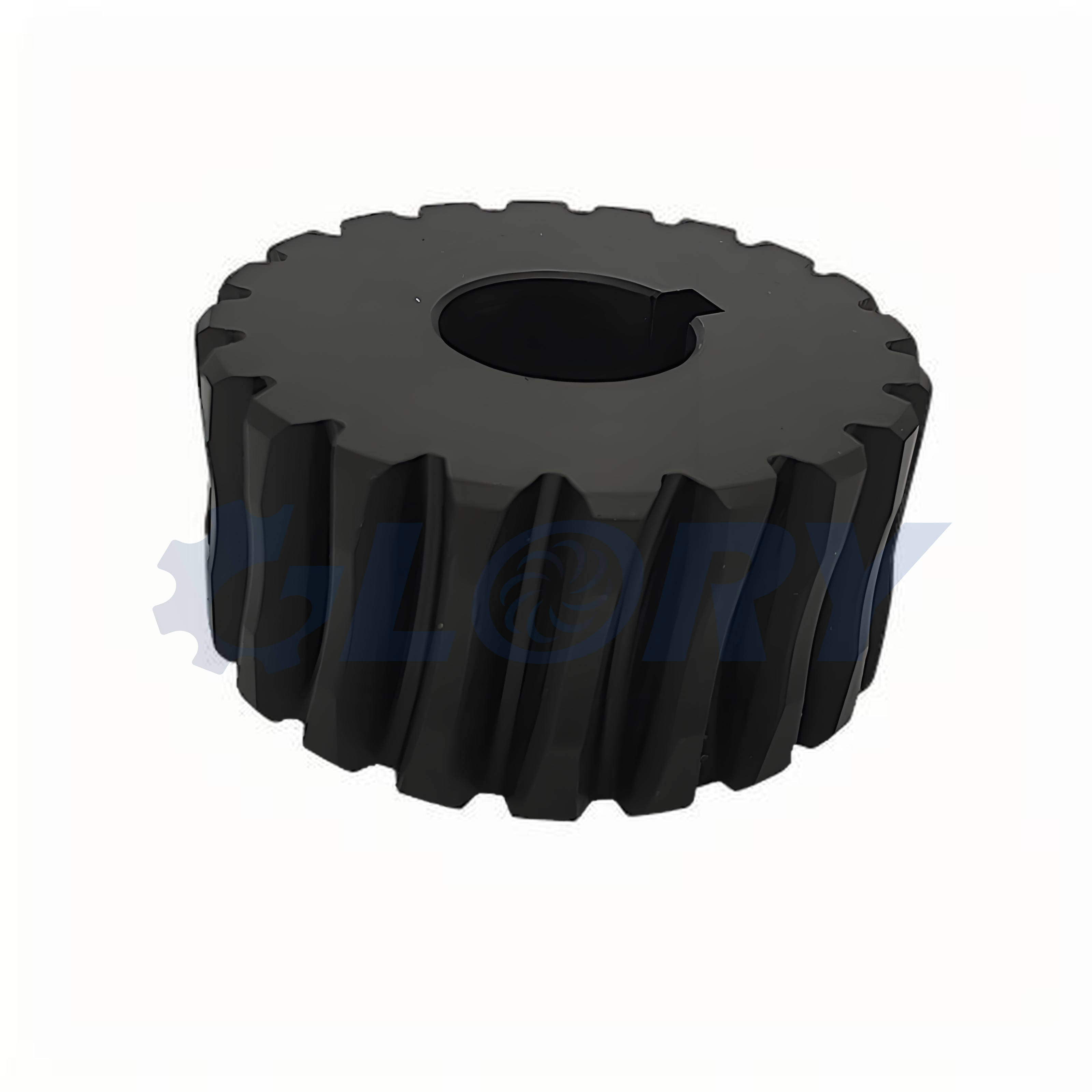