Machining of Aluminum Profile Heat Sinks
Machining aluminum profile heat sinks is a common custom part process, widely used in industries such as electronics, electrical appliances, and automobiles for effective heat dissipation. Aluminum profiles are ideal for manufacturing heat sinks due to their excellent thermal conductivity, lightweight, and ease of machining.
1. Advantages of Aluminum Profile Heat Sinks
- Excellent Thermal Conductivity: Aluminum has outstanding thermal conductivity, which helps quickly transfer heat away from devices.
- Lightweight: With a low density, aluminum helps reduce the overall weight of devices, which is especially beneficial in lightweight designs such as electronic equipment and automobiles.
- Corrosion Resistance: Anodized aluminum heat sinks offer good corrosion resistance, making them suitable for harsh environments.
- Cost-Effective: Compared to other heat dissipation materials like copper, aluminum is more affordable, offering a high cost-performance ratio.
2. Heat Sink Machining Process
The process of machining aluminum profile heat sinks typically involves the following steps:
2.1 Extrusion
Aluminum heat sinks are usually formed by extrusion, where aluminum is extruded through a mold to create the desired profile shape, including fin structures. Extrusion allows for complex geometries that maximize heat dissipation efficiency.
2.2 CNC Machining
CNC machines are used to perform precise machining on aluminum heat sinks, ensuring dimensional tolerances and surface quality. The main machining tasks include:
- Drilling: Providing positioning holes or threaded holes for heat sink installation.
- Cutting and Trimming: Cutting the heat sinks to different sizes according to customer needs and trimming the edges.
- Milling: Machining specific areas to ensure flatness and precision on the contact surfaces, enhancing thermal conductivity.
2.3 Surface Treatment
To improve the performance and appearance of aluminum heat sinks, surface treatment is necessary. Common surface treatments include:
- Anodizing: Enhances the corrosion resistance of the heat sink while improving its appearance.
- Coating or Electrophoretic Painting: Increases weather resistance and wear resistance.
2.4 Assembly and Quality Control
After machining, the heat sinks undergo rigorous quality checks, including dimension checks, fin thickness, and spacing control to ensure optimal heat dissipation and precise assembly.
3. Applications of Aluminum Heat Sinks
Aluminum profile heat sinks are widely used in the following fields:
- Electronic Products: Used in high-heat-generating electronic components such as LED lights and power devices.
- Automotive Industry: Applied in electric vehicle battery management systems, in-vehicle electronics, and more.
- Power Equipment: Heat sinks for equipment like inverters and power modules.
- Telecommunications: Heat dissipation modules for 5G base stations.
4. Design Considerations
When designing aluminum profile heat sinks, the following factors should be taken into account:
- Fin Spacing and Thickness: These affect the efficiency of heat dissipation and airflow. Fins spaced too closely can restrict airflow, while too wide spacing reduces efficiency.
- Surface Area: Increasing the number of fins or extending the length of the fins can increase the surface area, thereby improving heat dissipation efficiency.
- Mounting Method: The design should facilitate easy installation and fixing to ensure stable performance.
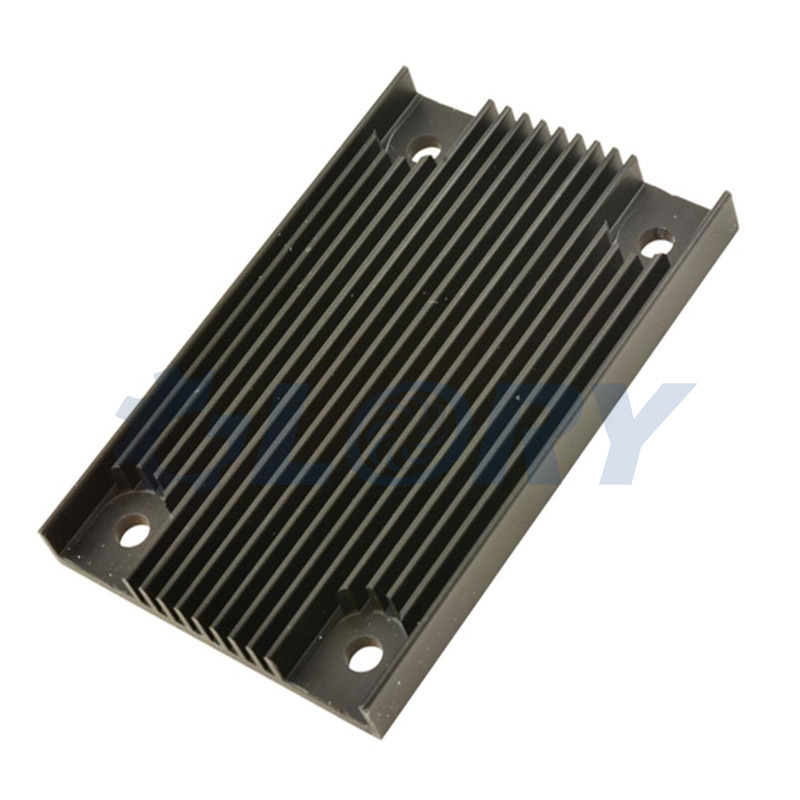